Im Überblick
In Produktionsbetrieben können Maschinenstillstände und damit verbundene Ausfallzeiten mit sehr hohen Kosten verbunden sein. Die sogenannte zustandsorientierte Instandhaltung kann vorbeugen.
Je nach „Sensibilität“ der Produktionsprozesse und den daraus resultierenden Folgen bei einem ungeplanten Produktionsstillstand können die Kosten pro Stunde durchaus im sechsstelligen Bereich liegen. Ist die Wiederinbetriebnahme der Anlage z. B. aufgrund fehlender Ersatzteile nicht zeitnah möglich, können die Auswirkungen bei einem mehrtägigen Ausfall für ein Unternehmen durchaus existenzgefährdend sein. Die möglichen Folgekosten setzen sich aus verschiedenen Posten zusammen und unterscheiden sich je nach Branche. Hier einige typische Kosten:
Unmittelbare Kosten, die sich aus Ausfallzeit, der durchschnittlichen Produktionsrate pro Stunde, den nicht produzierten Einheiten und dem Bruttogewinn pro Einheit zusammensetzen.
Kosten für Reparatur und Wiederinbetriebnahme durch einen oder mehrere technische Mitarbeiter, die die Anlage nach erfolgter Instandsetzung auch wieder in Betrieb nehmen.
Kosten für Produktionsmitarbeiter, die weiterbezahlt werden müssen, obwohl sie ihrer Arbeit an der jeweiligen Maschine oder Anlage nicht weiter nachgehen können.
Weitere Kosten wie etwa der Fehleridentifizierung, Kosten durch Implementierungvon vorübergehenden Abhilfemaßnahmen während des Stillstands, Kosten durch externe Experten, die zur Problemlösung hinzugezogen werden müssen, sowie entgangene Gesamteinnahmen.
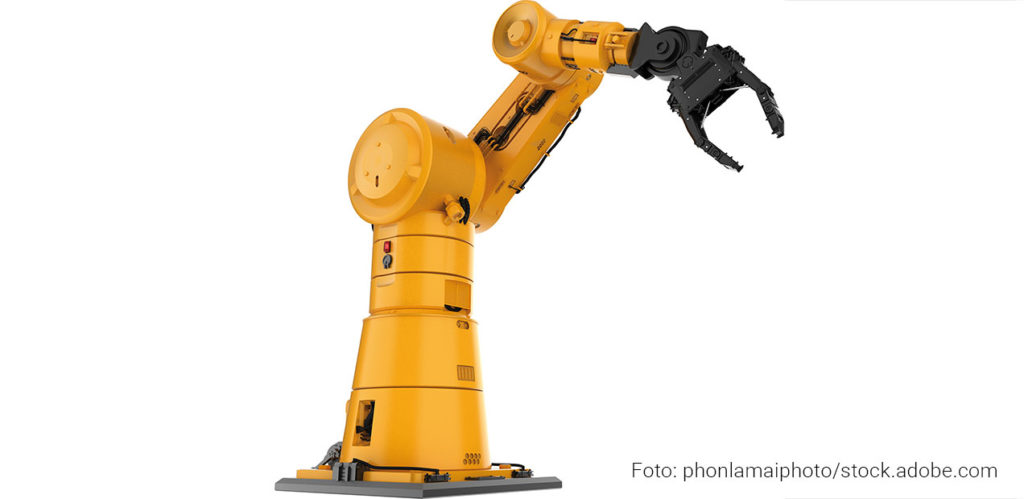
Gründe für einen Maschinenstillstand
Sie können vielfältig sein, z. B.: Keine existierenden Instandhaltungsstrategien und daraus resultierend fehlende Wartung, schlechte Netzqualität und unsichere Versorgungssicherheit. Oder schlicht menschliches Versagen.
Und Gegenstrategien
Um Maschinenstillstände zu vermeiden bzw. die Wahrscheinlichkeit eines Ausfalls möglichst gering zu halten, existieren je nach Branche unterschiedliche Strategien. Die herkömmliche „konservative Instandhaltungsmethode“, die nach einem festen Zeitplan Verschleiß- und Maschinenteile ausnahmslos austauscht, wird in modernen Produktionsbetrieben immer mehr durch die „zustandsorientierte Instandhaltung“ abgelöst.
Bei dieser Methode werden Maschinen mit unterschiedlichen Sensoren ausgestattet, um den Ist-Zustand der Anlage kontinuierlich zu überwachen. Das können ganz triviale Betriebsstundenzähler oder auch Temperatur-, Druck-, Durchfluss- und Vibrationssensoren sein oder auch komplexe Energie-Monitoringsysteme und Analysen der Netzqualität. Diese Daten lassen sich bei entsprechender Vernetzung auch ortsunabhängig abrufen. Maschinen sind damit weltweit überwachungsfähig.
Eine für alles geeignete, generelle Instandhaltungsstrategie gibt es freilich nicht. Je nach Branche, Sensibilität des Prozesses und den resultierenden Kosten bei einem Anlagenausfall sollte jedes Unternehmen eine für sich passende Strategie erarbeiten. Dafür sollten unbedingt auch die Kosten der vorbeugenden Instandhaltungsmaßnahme den Kosten eines möglichen Ausfalls gegenübergestellt werden.
Der Beitrag ist ursprünglich im Sonepar-Report der Ausgabe Mai auf den Seiten 10/11 erschienen.
Neuste Beiträge
- Türsteher, Feuerwehr oder Bodyguard – Wie schützen Sie Ihre Daten und Hardware?
- Effizient, nachhaltig und zukunftssicher? – Smarte Wärmeregulierung im Faktencheck
- Wie riskant ist der Traum von der Selbstständigkeit?
- Datenmüll als Klimakiller – die unsichtbare Gefahr
- Sonepar-Sustainability Week: Möglichmacher für Klima- und Umweltschutz.